Profile
About PT. KAWAI NIP
Quality Statement
To our customers, we pledge quality products and superior service. We will establish lasting partnerships with our customers and strive to meet their expectations 100% of the time.
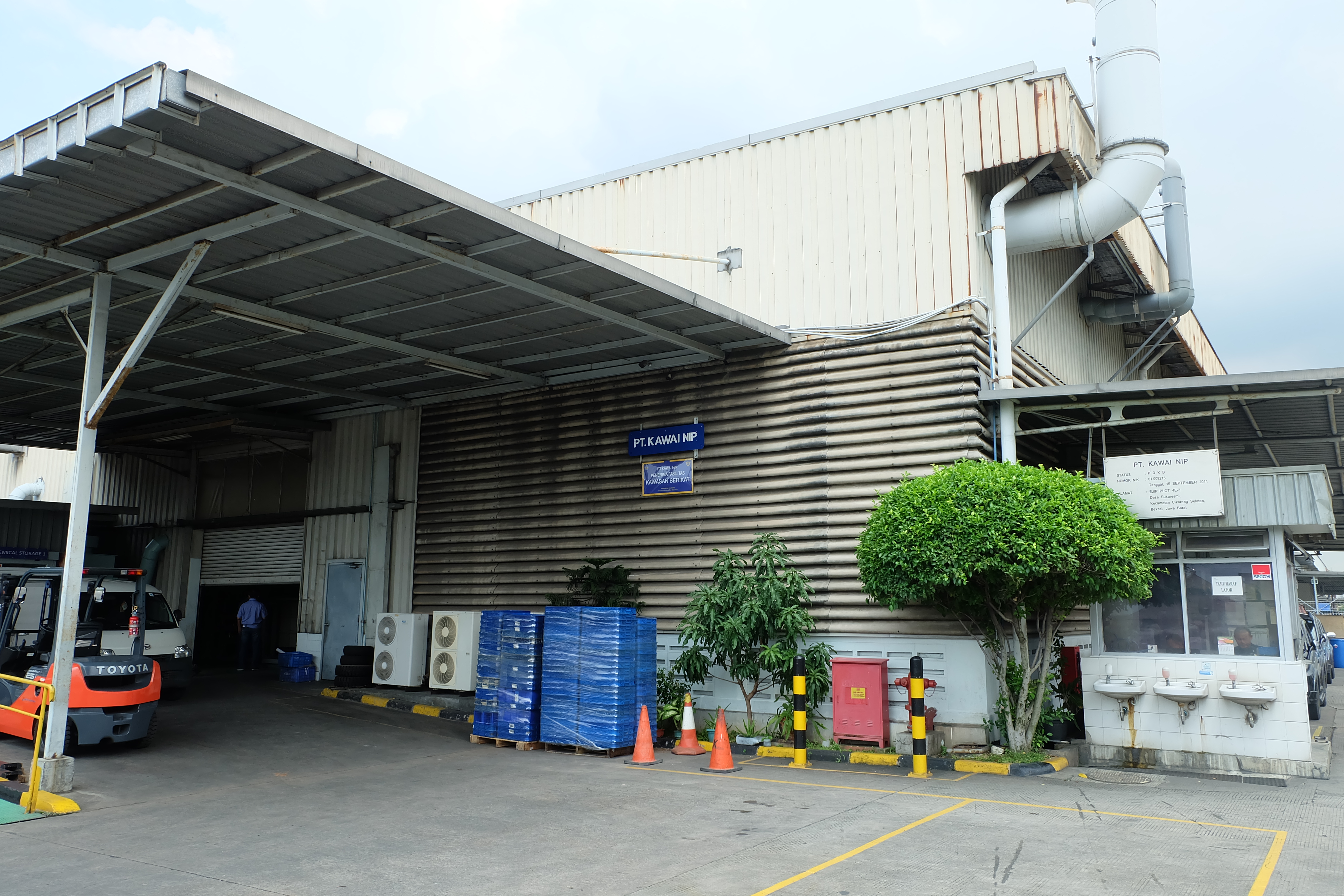
PT. KAWAI NIP still has certifications of ISO 9001 and ISO 14001 (Version 2015).
PT. KAWAI NIP is increasing quality and total production management.
ISO 9001
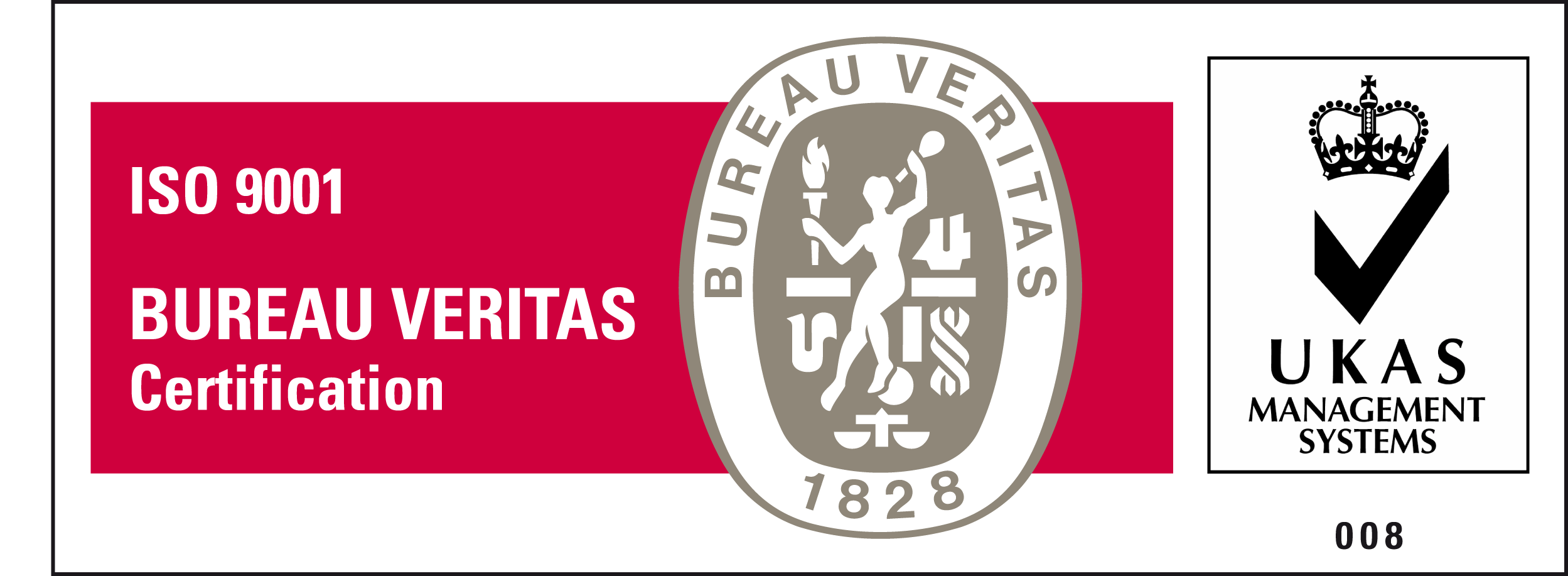
ISO 14001
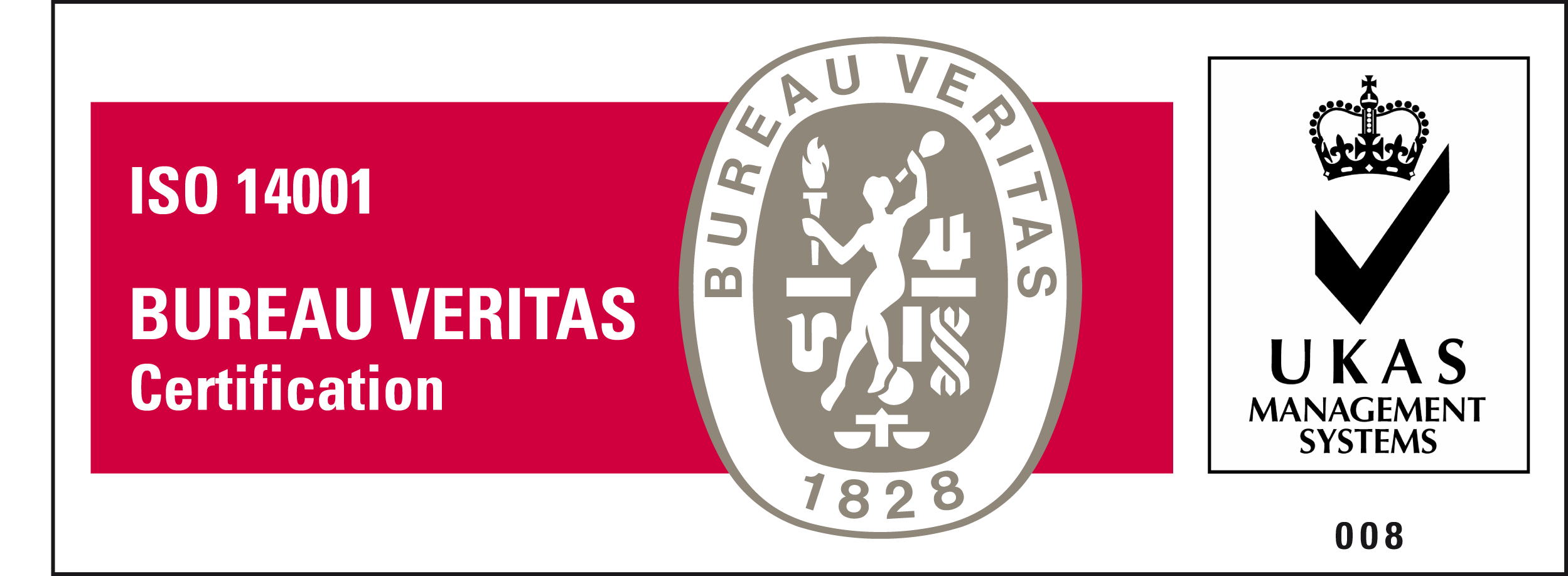
Information
Features of Proper to Electroless Nickel Plating
- Possible to control thickness of Nickel Plating less than few micron millimeters.
- Very little thickness margin of error on an around the parts.
- Available to increase hardness using process of the heat treatment. (Electric Nickel Plating is not available this process)
- Anti corrosion and Hardness are superior to an Electric Nickel Plating.
- Electrical resistance and Luster are less than an Electric Nickel Plating.
About Electroless Nickel Plating
Non Electrical Plating of Metals and Plastics to achieve uniform coatings by a process of controlled autocatalytic (self-continuing) reduction. Discovered in 1944 by A. Brenner and G.E Riddell, electroless plating involves the deposition of such metal as copper, nickel, silver, gold, or palladium on the surface of variety of materials by means of a reducing chemical bath. It is also used in mirroring, in which a clean surface of glass is dipped into an ammoniacal silver solution mixed with Rochelle salt or with a nitric acid cane-sugar alcohol solution. Nonmetallic surfaces, such as plastics, must be chemically treated prior to electroless plating. The Major expansion of Electroless Plating has come in the area of plastics, as in the plating of printed electronic circuits. A large number of consumer goods are coated by this method to create durable and attractive surfaces.
The biggest advantage of electroless nickel plating verses standard nickel plating is that it covers the entire part with a uniform thickness coating, including seams, sharp edges, and the interior of deep drawn parts.
Unlike standard nickel plating which relies on current density in a bath for deposit thickness, the thickness of electroless nickel palting depends solely on the deposition rate and the length of time in the solution. Because of these properties highly accurate and repeatable thicknesses can be obtained making electroless nickel the preferred choice when full part tolerances are critical.
What is Electroless Nickel Plating ?
Electroless Nickel Plating is an auto-catalytic reaction used to deposit a coating of nickel on a substrate. Unlike electroplating, it is not necessary to pass an electric current through the solution to form a deposit. This plating technique is to prevent corrosion and wear. Electroless Nickel Plating has several advantages versus Electro Plating. Free form flux-density and power supply issues, it provides an even deposit regardless of workpiece geometry, and with the proper pre-plate catalyst, can deposit on non-conductive surfaces. In general, electroplating improves a wide range of characteristics not inherently present in the base material.
Some of these benefits include :
- Increased resistance to corrosion
- Improved Hardness
- Superior Strength
- Resistance to wear
- Improved Ductility
Electroless Nickel Plating Application :
- It is commonly used in Engineering coating applications where wear resistance, hardness and corrosion protection are required. Applications include rotors, drive shafts, paper handling equipment, electrical and mechanical tools and office equipment.
- Due to the high hardness of the coating it can be used to salvage worn parts. Coatings up to 15 micrometers can be applied. Its uniform deposition profile mean it can be applied to complex components not readily suited to other hard wearing coatings like hard chromium. Its use in the automotive industry for wear resistance has increased significantly.